Содержание
Коленвал Д-245 укладка
Перед сборкой каждый коленчатый вал должен быть проверен на магнитном или ультразвуковом дефектоскопе на отсутствие микро и макротрещин; а также на соответствие подобранного комплекта вкладышей коренных подшипников размеру коренных шеек
Механические повреждения (риски, вмятины, забоины и др.) на шейках коленчатого вала и вкладышах коренных подшипников не допускаются.
Коренные шейки, вкладыши и гнезда подшипников надо протереть салфеткой и продуть сжатым воздухом.
Крышки коренных подшипников должны плотно входить в гнезда блока.
Перестановка и перевертывание крышек коренных подшипников не допускаются.
Раскомплектовка вкладышей коренных подшипников не допускается.
Вкладыши должны быть установлены в соответствующие гнезда блока цилиндров.
Коренные шейки и вкладыши перед укладкой коленчатого вала надо смазать моторным маслом.
Упорные полукольца, устанавливаемые на стенки постели пятой коренной опоры и крышки подшипника, должны быть подобраны так, чтобы продольный люфт коленчатого вала после затяжки болтов коренных подшипников составлял 0,14…0,37 мм.
Сухари клапанного механизма должны выступать над плоскостью шайбы на 0,5…2,0 мм;
В комплект на один дизель надо подбирать поршни, шатуны и поршневые пальцы одинаковой весовой группы, разновес шатунов в комплекте с поршнями не должен превышать 30 г.
Коренные и шатунные шейки и вкладыши подшипников коленчатого вала изготовляются двух номинальных размеров.
Номинальные размеры шеек коленчатого вала
Обозначение
|
Диаметр шейки вала, мм
| |
---|---|---|
Коренной
|
шатунной
| |
1Н
|
75,25-0,083
|
68,25-0,077
|
2Н
|
75,00-0,083
|
68,00-0,077
|
Номинальные размеры вкладышей подшипников коленчатого вала
Обозначение
|
Внутренний диаметр вкладыша, мм
| |
---|---|---|
Коренной шейки
|
Шатунной шейки
| |
БН1
|
75,25-0,033
|
68,25+0,025
|
БН2
|
75,00-0,033
|
68,00+0,025
|
Коленчатые валы, шатунные и коренные шейки которых изготовлены по размеру второго номинала, имеют на первой щеке дополнительное обозначение:
- 2К — коренные шейки второго номинала;
- 2Ш — шатунные шейки второго номинала;
- 2КШ — шатунные и коренные шейки второго номинала.
Ремонтные размеры шеек коленчатого вала
Обозначение
|
Диаметр шейки вала, мм
| |
---|---|---|
Коренной
|
шатунной
| |
Д1
|
74,75-0,083
|
67,75-0,077
|
Р1
|
74,50-0,083
|
67,50-0,077
|
Д2
|
74,25-0,083
|
67,25-0,077
|
Р2
|
74,00-0,083
|
67,00-0,077
|
Д3
|
73,75-0,083
|
66,75-0,077
|
Р3
|
73,50-0,083
|
66,50-0,077
|
Д4
|
73,25-0,083
|
66,25-0,077
|
Р4
|
73,00-0,083
|
66,00-0,077
|
При проверке затяжки болтов крепления крышек коренных подшипников на доворачивание величина крутящего момента не должна превышать 240 Нм.
Момент затяжки болтов крепления коренных подшипников должен быть 200…220 Нм.
При этом коленчатый вал должен плавно, без заеданий, проворачиваться моментом не более 3 Нм.
содержание .![]() Проверка затяжки болтов крепления головки цилиндров Проверку затяжки болтов крепления головки цилиндров производите по окончании обкатки и через каждые 40 тыс. км пробега на прогретом дизеле в следующем порядке:
После проверки затяжки болтов крепления головки цилиндров установите на место ось коромысел и отрегулируйте зазор между клапанами и коромыслами. Рисунок 2 — Регулировка зазора в клапанах. Регулировку производите в следующей последовательности: — снимите колпак крышки головки цилиндров и проверьте крепление стоек оси коромысел; — проверните коленчатый вал до момента перекрытия клапанов в первом цилиндре (впускной клапан первого цилиндра начинает открываться, а выпускной заканчивает закрываться) и отрегулируйте зазоры в четвертом, шестом, седьмом и восьмом клапанах (считая от вентилятора), затем поверните коленчатый вал на один оборот, установив перекрытие в четвертом цилиндре, и отрегулируйте зазоры в первом, втором, третьем и пятом клапанах. Для регулировки зазора отпустите контргайку винта на коромысле регулируемого клапана в соответствии с рисунком 2 и, поворачивая винт, установите необходимый зазор по щупу между бойком коромысла и торцом стержня клапана. После установки зазора затяните контргайку. По окончании регулировки зазора в клапанах поставьте на место колпак крышки головки цилиндров. содержание .. 130 131 132 133 134 135 136 137 138 139 140 .. |
Таблица моментов затяжки фланцевых болтов
Последовательность и момент затяжки
Фланцевые соединения требуют надлежащей затяжки во избежание утечки жидкости из соединения. Последовательность затяжки болтов или последовательность крутящего момента определяется в процедуре затяжки крутящим моментом. У большинства компаний есть своя процедура затяжки фланцевых болтов, используемая во время строительства и эксплуатации завода.
Фланцевые соединения затягиваются с помощью динамометрического ключа (ручного или гидравлического ключа). Прижимная нагрузка, возникающая при затяжке, превышает 75 % расчетной нагрузки крепежного изделия. Чтобы воспользоваться преимуществами предварительной нагрузки, усилие зажима в винте должно быть выше, чем усилие разделения соединения.
Если для нагрузки на болт требуется крутящий момент выше 678 Нм (500 футо-фунтов), рекомендуется использовать гидравлическую затяжку болтов.
Источник изображения — Fluid Power Technology
Величина крутящего момента зависит от трения между резьбой шпильки и головкой гайки, на это трение можно повлиять путем нанесения смазки или любого покрытия (например, кадмия или цинка), нанесенного на шпильки. Стандарт болтовых соединений определяет, относится ли значение крутящего момента к сухой или смазанной резьбе шпильки/болта. Если затягивается болт, а не гайка, то значение крутящего момента следует увеличить, чтобы компенсировать дополнительное трение – болты следует затягивать только в том случае, если они установлены в отверстиях с зазором.
Болты следует затягивать с контролем крутящего момента, используя противозадирную смазку, такую как Molykote или аналогичную, перед установкой. Указанный способ затяжки болтов одинаково применим к болтам с покрытием, оцинкованным и неоцинкованным.
Фланцевая шпилька Момент затяжки Последовательность очень важна для правильной затяжки фланцевого соединения. В этой подробной статье я попытался упростить эту последовательность затяжки, чтобы вы достигли желаемого результата, не повредив фланец и шпильки.
Предварительная проверка затяжки болтов
Состояние фланцев
- Проверьте состояние поверхностей фланцев на наличие царапин, грязи и окалины.
- Проверьте на наличие точечной коррозии и следов инструмента.
- Осмотрите посадочные поверхности прокладки.
- Проверьте участки на фланце, где будут сидеть гайки, они должны быть плоскими, без точечной коррозии и чрезмерного износа.
- RTJ должны содержаться в чистоте, без коррозии и повреждений.
Канавки
Допустимые дефекты выступа фланца трубы указаны в ASME 16.5, таблица 3. См. таблицу Допустимые дефекты отделки поверхности фланца для фланца с выступом.
Размер в дюймах | Размер в мм | Максимальная радиальная проекция дефектов | |
---|---|---|---|
Не глубже основания зубцов, мм | Глубже нижней части зубцов, мм | ||
1/2 | 15 | 3,0 | 1,5 |
3/4 | 20 | 3,0 | 1,5 |
1 | 25 | 3,0 | 1,5 |
1 1/4 | 32 | 3,0 | 1,5 |
1 1/2 | 40 | 3,0 | 1,5 |
2 | 50 | 3,0 | 1,5 |
2 1/2 | 65 | 3,0 | 1,5 |
3 | 80 | 4,5 | 1,5 |
3 1/2 | 90 | 6,0 | 3,0 |
4 | 100 | 6,0 | 3,0 |
5 | 125 | 6,0 | 3,0 |
6 | 150 | 6,0 | 3,0 |
8 | 200 | 8,0 | 4,5 |
10 | 250 | 8,0 | 4,5 |
12 | 300 | 8,0 | 4,5 |
14 | 350 | 8,0 | 4,5 |
16 | 400 | 10,0 | 4,5 |
18 | 450 | 12,0 | 6,0 |
20 | 500 | 12,0 | 6,0 |
24 | 600 | 12,0 | 6,0 |
Тест по фланцам и олетам – проверьте себя, пройдите этот тест
Проверка соосности фланцев.
Визуально проверьте выравнивание фланцев, чтобы убедиться в том, что получена приемлемая посадка. При центровке фланцев следите за тем, чтобы в стыке не было остаточных напряжений. Использование термокоррекции для выравнивания фланцев не рекомендуется и должно быть строго запрещено.
- Поверхности фланцев должны быть параллельны и выровнены.
- Отверстия под болты во фланце должны располагаться на одной линии, чтобы болты проходили свободно.
Проверка гаек, шпилек или болтов
- Визуально осмотрите гайки и шпильки/болты перед установкой, чтобы убедиться в отсутствии дефектов, таких как коррозия, поврежденная резьба и т. д. Не следует использовать гайки-болты с поврежденной резьбой.
- Проверьте длину шпильки или болта, чтобы избежать коротких болтов и чрезмерной резьбы. Фланцевые болты должны иметь недостаточную длину, чтобы можно было использовать оборудование для натяжения болтов или лопатки, прокладки, капельные кольца и межфланцевые клапаны, а также соответствующие дополнительные прокладки.
- Осмотрите шпильки и гайки после очистки, чтобы убедиться, что на них нет заусенцев. Шпильки и гайки следует очистить с помощью проволочной щетки, чтобы удалить грязь с резьбы. Смазка (MOLYKOTE) должна быть нанесена на резьбу и гайки на контактные поверхности фланцев. Смазка не должна использоваться в прокладке и в зоне посадки прокладки.
- Марки материала болтов и гаек должны быть правильно идентифицированы перед их использованием.
- Болты и гайки можно использовать повторно только в том случае, если известно, что они не подвергались перегрузке и не превышали свой предел текучести.
- Идентификационная маркировка гайки всегда должна быть направлена наружу при установке гайки на болт.
Проверка прокладки
- Не используйте герметик, смазку или другую пасту или клей на поверхности прокладки или фланца.
- При установке прокладки она не должна вдавливаться в гнездо прокладки между сопрягаемыми поверхностями фланцев.
После того, как прокладка установлена, сопрягаемые фланцы осторожно соединяют вместе, не стряхивая прокладку с седла, устанавливают все шпильки и вручную затягивают все гайки.
- Визуально осмотрите прокладки перед установкой, чтобы убедиться в отсутствии дефектов.
- Цветовая маркировка должна соответствовать норме и типу прокладки, предоставленной производителем.
- Очистите посадочную поверхность прокладки проволочной щеткой.
- Убедитесь, что материал соответствует указанному; ищите любые возможные дефекты или повреждения прокладки, такие как складки или заломы.
- Все прокладки из мягкого материала следует заменять новыми всякий раз, когда открытый стык необходимо снова закрыть.
- Спирально-навитая прокладка должна использоваться только один раз.
Последовательность затяжки фланцевых болтов
После завершения всех предварительных проверок. Вы можете продолжить затяжку шпильки в заранее определенной последовательности крутящего момента, упомянутой здесь. Затяните болты и гайки в последовательности «КРЕСТ-КРЕСТ», используя как минимум три прохода затяжки и максимальное усилие болта, как определено.
- ПРОХОД 1 Последовательность крутящего момента: крутящий момент не более 30 % от конечного значения крутящего момента в соответствии с последовательностью крутящего момента. Убедитесь, что прокладка сжимается равномерно.
- PASS 2 Последовательность крутящего момента: крутящий момент не более 60 % от конечного значения крутящего момента.
- PASS 3 Torque Sequence: крутящий момент до конечного значения крутящего момента (100 %).
После завершения трех основных проходов крутящего момента повторите затяжку гаек по крайней мере один раз, используя окончательный крутящий момент «КРЕСТ-КРЕСТ», пока гайка не перестанет вращаться.
Для удобства нумерация болтов должна быть выполнена по часовой стрелке вокруг фланца в следующей последовательности.
В таблице ниже показана последовательность крутящего момента для фланцев с болтами от 4 до 32.
Количество болтов/шпилек | Последовательность затяжки болтов |
---|---|
Фланец с 4 болтами | 1,3,2,4 |
8 болтов Фланец | 1,5,3,7,2,6,4,8 |
12 болтов Фланец | 1,7,4,10,2,8,5,11,3,9,6,12 |
16 болтов Фланец | 1,9,5,13,3,11,7,15,2,10,6,14,4,12,8,16 |
20 болтов Фланец | 1,11,6,16,3,13,8,18,5,15,10,20,2,12,7,17,4,14,9,19 |
24 болта Фланец | 1,13,7,19,4,16,10,22,2,14,8,20,5,17,11,23,6,18,12,24,3,15,9,21 |
28 болт Фланец | 1,15,8,22,4,18,11,25,6,20,13,27,2,16,9,23,5,19,12,26,3,17,10,24,7 ,21,14,28 |
32 болта Фланец | 1,17,9,25,5,21,13,29,3,19,11,27,7,23,15,31,2,18,10,26,6,22,14,30,8 ,24,16,32,4,20,12,28 |
Таблица крутящих моментов для фланцев класса 150 ASTM A694 класс F52

фунт/дюйм2
lbf.ft.
Нм
Таблица крутящих моментов для фланцев класса 300 ASTM A694 класс F52
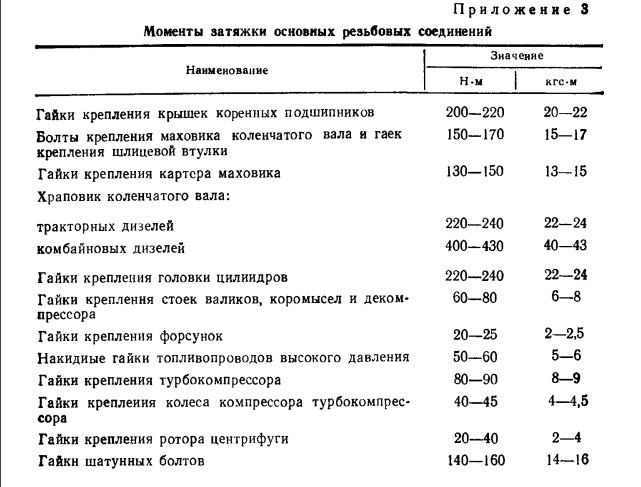
фунт/дюйм2
lbf.ft.
Нм
Таблица крутящего момента для фланца класса 600 9
90 037
фунт/дюйм2
lbf.ft.
Нм
Таблица крутящих моментов для фланцев класса 900 ASTM A694 марки F52, F60 и F65

фунт/дюйм2
lbf.ft.
Нм
Таблица крутящего момента для фланца класса 1500
Материалы фланцев: ASTM A105, ASTM A182, сорта F50 и F51, ASTM A350, сорта LF2 и LF3, ASTM A694, сорта F52, F60 и F65 | |||||||
---|---|---|---|---|---|---|---|
Материалы болтовых соединений : ASTM A193, сорта B7 и B7M, ASTM A320, сорта L7, L7M и L43.![]() | |||||||
Тип прокладки: Спиральная навивка и кольцевое соединение | |||||||
Смазка для болтов Molykote 1000 (µ = 0,11) | |||||||
Размер в дюймах | Размер в мм | № болта | Диаметр болта. | Тип резьбы | Напряжение болта фунт/дюйм2 | Крутящий момент lbf.ft. | Крутящий момент Нм |
1/2 | 15 | 4 | ½” | УНК | 40 000 | 121 | 165 |
3/4 | 20 | 4 | ½” | УНК | 45 000 | 137 | 185 |
1 | 35 | 4 | ½” | УНК | 45 000 | 218 | 296 |
1 ½ | 40 | 4 | ½” | УНК | 50 000 | 361 | 489 |
2 | 50 | 4 | 5/8” | УНК | 50 000 | 243 | 329 |
3 | 80 | 4 | 5/8” | УНК | 50 000 | 526 | 714 |
4 | 100 | 8 | 5/8” | УНК | 50 000 | 735 | 997 |
6 | 150 | 8 | ¾” | УНК | 50 000 | 994 | 1347 |
8 | 200 | 8 | ¾” | УНК | 50 000 | 1675 | 2271 |
10 | 250 | 12 | 7/8” | УНК | 50 000 | 2615 | 3545 |
12 | 300 | 12 | 7/8” | УНК | 50 000 | 3193 | 4329 |
14 | 350 | 12 | 1 дюйм | ООН8 | 45 000 | 4133 | 5603 |
16 | 400 | 16 | 1 дюйм | ООН8 | 45 000 | 5713 | 7746 |
18 | 450 | 16 | 1 1/8” | ООН8 | 45 000 | 7652 | 10375 |
20 | 500 | 20 | 1 1/8” | ООН8 | 45 000 | 9986 | 13539 |
24 | 600 | 20 | 1 ¼” | ООН8 | 45 000 | 15983 | 21670 |
Материалы болтовых соединений: ASTM A193, сорта B7 и B7M, ASTM A320, сорта L7, L7M и L43.![]() | |||||||
Тип прокладки: Спирально-навитое и кольцевое соединение | |||||||
Смазка для болтов Molykote 1000 (µ = 0,11) | |||||||
Размер в дюймах | Размер в мм | № болта | Болт диам. | Тип резьбы | Напряжение болта фунт/дюйм2 | Крутящий момент lbf.ft. | Крутящий момент Нм |
1/2 | 15 | 4 | ½” | УНК | 45 000 | 137 | 185 |
3/4 | 20 | 4 | ½” | УНК | 50 000 | 152 | 206 |
1 | 35 | 4 | ½” | УНК | 50 000 | 243 | 329 |
1 ½ | 40 | 4 | ½” | УНК | 55 000 | 579 | 785 |
2 | 50 | 4 | 5/8” | УНК | 55 000 | 397 | 538 |
3 | 80 | 4 | 5/8” | УНК | 55 000 | 809 | 1097 |
4 | 100 | 8 | 5/8” | УНК | 55 000 | 1436 | 1947 |
6 | 150 | 8 | ¾” | УНК | 50 000 | 3195 | 4332 |
8 | 200 | 8 | ¾” | УНК | 50 000 | 3195 | 4332 |
10 | 250 | 12 | 7/8” | УНК | 50 000 | 6348 | 8606 |
12 | 300 | 12 | 7/8” | УНК | 50 000 | 8502 | 11527 |
Отказ от ответственности. Перед использованием проконсультируйтесь с профессиональным инженером.
Вы мастер по компонентам трубопроводов?
Как пользоваться динамометрическим ключом
Вот как я понял, что мне нужно научиться пользоваться динамометрическим ключом: Это был канун Рождества, и я избегал своей семьи, работая над своим джипом.
Стекло на задней двери открывалось каждый раз, когда я наезжал на кочку, прижимал стеклоочиститель, пропускал воду, а в сухие дни издавал скрип стекла по пластику, заставляющий меня молиться о дожде. Я искал проблему в Интернете, и оказалось, что все, что мне нужно было сделать, это ослабить болты, крепящие стекло к петлям, сдвинуть стекло на крошечную долю дюйма вниз и снова затянуть их.
Когда стекло висит немного ниже, оно не выскочит. Достаточно просто. И я прошел весь путь до повторной затяжки без происшествий.
Но потом, стоя под приподнятым стеклом и рассеянно наблюдая за людьми, прогуливающимися по парку через улицу, я повернул гаечный ключ слишком сильно. Раздался громкий треск, и в мгновение ока на месте стекла стало небо, а меня покрыло миллионом крошечных осколков. Пришлось звать на помощь своих. Карма.
Прочитать это
- Как я построил машину своей мечты
Моя ошибка? Я должен был использовать динамометрический ключ, тип гаечного ключа, который точно показывает, какое усилие вы прикладываете к застежке, чтобы вы не затягивали чрезмерно (или недостаточно). В моей ситуации не было стереотипного использования — динамометрические ключи гораздо чаще применяются для затягивания гаек. Но дело в том, что они являются незаменимыми инструментами для механиков, потому что каждый крепеж в вашем автомобиле, в том числе, да, на стекле двери багажного отделения, имеет определенный номинальный крутящий момент. Вот как использовать динамометрический ключ.
Слишком много значит слишком много
Производители автомобилей указывают надлежащий уровень затяжки, значение крутящего момента, выраженное в футо-фунтах, которое обычно можно найти в руководстве по эксплуатации вашего автомобиля. Крутящий момент — это сила вращения, приложенная к точке или, в данном случае, к гайке. Наденьте на гайку гаечный ключ длиной 1 фут и приложите усилие 10 фунтов к противоположному концу. Теперь вы крутите эту гайку с 10 ft-lb (расстояние, умноженное на силу, или 1 фут, умноженный на 10 фунтов). Используйте гаечный ключ длиной 2 фута и приложите 50 фунтов силы, и вы получите 100 футо-фунтов, что, к счастью, примерно столько же, сколько у большинства гаечных ключей, и столько силы, сколько большинство локтей счастливы провернуть. .
В то время как большинство механиков полагаются на хорошо откалиброванное колено, чтобы затянуть вещи, жизненно важно, чтобы затяжка застежки находилась в довольно узком диапазоне. Слишком слабо, и есть опасность самопроизвольного откручивания гайки или болта по дороге. Или, возможно, протечет прокладка или уплотнительное кольцо, зажатое этим болтом. Слишком затянуты и есть другие риски: скрепленная болтами часть может быть сжата, согнута или повреждена иным образом. Стержень болта может сломаться, или резьба может сорваться, что приведет к полному отсутствию зажимного усилия. Лучше всего затягивать крепеж с помощью устройства, называемого динамометрическим ключом.
Основы
Почему бы нам просто не затянуть каждый крепеж любого размера с одинаковым значением крутящего момента? Зачем нам руководство по ремонту, чтобы сказать нам, что один 5/16-дюймовый болт, удерживающий крышку клапана, требует 11 футо-фунтов, а 5/16-дюймовая шпилька на амортизаторе требует 20?
Давайте обсудим, что происходит, когда вы поворачиваете головку гайки или болта. Резьба представляет собой форму наклонной плоскости или клина, самый простой тип инструмента. Поскольку наклонная плоскость вклинивается (поворачивается) в резьбу, она прикладывает усилие по длине болта, фактически превращая болт в пружину растяжения. Это напряжение в стержне болта скрепляет две детали вместе. Если сила зажима больше, чем нагрузка, действующая, скажем, между головкой и блоком, эти две детали никогда не ослабнут самопроизвольно.
И чем большее усилие закручивания вы прикладываете к головке болта или гайки, тем больше усилие прижима в соединении. Так что просто затяните его, пока он не ослабнет, верно?
Похожие статьи
- Лучшие аккумуляторные ударные гайковерты
Неправильно. Различия в общей длине болта, материале зажимаемых частей, наличии прокладки между двумя частями и даже сплаве самого болта влияют на правильный крутящий момент.
Кроме того, правильное значение крутящего момента учитывает трение между резьбами, которое является самой большой переменной, влияющей на взаимосвязь между крутящим моментом, приложенным к головке болта, и усилием зажима. Трение возникает из-за резьбы, а также из-за того, что вращающаяся поверхность болта царапает неподвижную заготовку.
Преодоление трения может составлять от нескольких процентов до 50 процентов усилия, необходимого при затягивании гайки или болта. А это значит, что усилие зажима может варьироваться в широких пределах, что не очень хорошо, когда вы устанавливаете головку блока цилиндров или впускной коллектор.
Ящик для инструментов: типы динамометрических ключей
Ben Kleiman
Bending-Beam
Этот ключ предназначен для тех, кому динамометрический ключ не требуется регулярно. Большая центральная балка сгибается при приложении крутящего момента, а несгибаемая стрела указателя позволяет напрямую считывать крутящий момент. Если он выходит из калибровки, просто согните указатель обратно до нуля с помощью плоскогубцев. Единственным самым большим недостатком является то, что ваше глазное яблоко должно быть припарковано прямо над указателем, пока вы читаете шкалу, что сложно в труднодоступных местах.
Микрометр «Clicker»
Этот профессиональный инструмент настроен на правильный крутящий момент и будет издавать тактильный и звуковой щелчок при достижении правильного крутящего момента. Он очень воспроизводим и точен, но его следует сбрасывать на ноль после каждого использования. Тем не менее, его следует регулярно калибровать, если он используется для критически важных деталей, таких как подвеска и внутренние крепления двигателя. Не используйте динамометрический ключ как храповик для разборки — сохраните его для окончательной сборки.
Бен Клейман
Ben Kleiman
Смазывать или нет
В большинстве случаев указанное значение крутящего момента предполагает наличие чистых и сухих деталей. Чистота означает отсутствие грязи, ржавчины, высохшего герметика или чего-либо, кроме блестящего металла.
Очистка резьбы проволочной щеткой поможет удалить ржавчину или герметик. Крепежные детали двигателя, такие как болты с головкой или болты с головкой, часто рекомендуется затягивать моторным маслом с вязкостью 30, смачивающим резьбу и шайбу. Если вы устанавливаете крепеж, который имеет спецификацию крутящего момента всухую, а резьба и поверхность болта смазаны маслом, вам нужно уменьшить крутящий момент на 15-25 процентов, потому что более скользкие поверхности уменьшат трение.
Смазочные материалы с тефлоновыми подшипниками или смазочные материалы на основе сульфида молибдена могут снизить трение настолько, что потребуется 50-процентное снижение момента затяжки. Даже простая замена болта или шайбы без покрытия болтом или шайбой с цинковым или кадированным покрытием требует, соответственно, снижения прилагаемого крутящего момента на 15 или 25 процентов, поскольку покрытие действует как смазка. Не прислушайтесь к этому совету, и застежка будет серьезно перетянута. Вы либо сломаете его, либо раздавите прокладку до точки, где она протекает.
Связанная статья
- Как восстановить ржавые старые инструменты
С другой стороны, ржавчина или заусенцы на резьбе могут увеличить трение настолько, что крепеж, затянутый до указанного значения, не обеспечит достаточного зажимного усилия. В инструкции по ремонту будет указано, должна ли застежка быть сухой или смазанной. В любом случае подготовьте болты. Не забывайте, что в остатках от мойки деталей или в банке с керосином, которую вы используете для очистки деталей, есть масло.
Даже быстрая струя сжатого воздуха для просушки крепежа оставит на нем маслянистую пленку, что повлияет на предельный крутящий момент. Если вы действительно привередливы, очистите аэрозольным карбюраторным или тормозным очистителем, а затем еще воздухом. Если вы использовали консистентную смазку или противозадирный состав, чтобы предотвратить заедание тормозных дисков ступицами, следите за тем, чтобы не загрязнить шпильки или зажимные гайки.
Момент-плюс-угол
Все чаще такие важные крепежные детали, как болты головки блока цилиндров, крепления крепления двигателя и болты впускного коллектора, требуют так называемой затяжки с моментом плюс угол. Из-за непостоянства трения между резьбой и поверхностью болта обычная затяжка крепежной детали недостаточно постоянна.
Разница в трении на несколько процентов из-за неравномерности резьбы, заусенцев, ржавчины или старого резьбового герметика может привести к огромной разнице в натяжении крепежа. Это может привести к самопроизвольному демонтажу соединения. Спецификация затяжки для этих креплений требует двух этапов.
Головка болта или гайка сначала затягивается — в обычной последовательности штриховки, если их больше двух — до предписанного значения крутящего момента; затем, снова начиная с первого болта, до второго, более высокого значения. Только после этого его следует повернуть одним плавным движением еще на несколько градусов. Единственный способ сделать это точно — использовать приспособление «крутящий момент плюс угол».
EPAUTO 1/2-дюймовый динамометрический ключ
EPAUTO 1/2-дюймовый 1/2-дюймовый динамометрический ключ
39 долларов на Amazon 35 долларов в Walmart
Кронштейн крепления привязывается к какому-либо соседнему объекту, чтобы закрепить транспортир, который должен быть возвращен к нулю после приложения начального крутящего момента. Затем ключ поворачивают на заданный дополнительный оборот. Опять же, это должно происходить в обычной последовательности для нескольких креплений.
Критически важные крепежные детали — болты с цилиндрической головкой — это дети с плакатов — настолько трудно правильно затянуть, что производитель не только указывает затяжку с усилием плюс угол, но и является одноразовым элементом, который необходимо выбросить. если он когда-либо будет удален. Эти болты с пределом текучести обычно имеют суженный прямой участок между резьбой и головкой болта.
При начальной затяжке болт растягивается по всей длине почти до предела упругой деформации. Если вы отвинтите болт в этот момент, он вернется к своей первоначальной длине. Приложите дополнительное вращение, и болт растянется до области пластической деформации, где дополнительное растяжение болта не дает дополнительной силы зажима, но позже болт не вернется к своей первоначальной длине.
Этот метод гарантирует, что все болты скрепят две детали вместе с почти одинаковым усилием, поэтому такие важные элементы, как прокладки головки блока цилиндров, не будут протекать. Вам, наверное, интересно, почему инженеры просто не используют болты большего размера, которые могут прикладывать достаточную силу без необратимой деформации. Эти большие болты могут быть перетянуты, а слишком сильное затягивание так же плохо или даже хуже, чем слишком легкое.
Закончили затяжку колес или ГБЦ? Не забудьте сохранить калибровку динамометрических ключей, установив микрометрическую шкалу на ноль, прежде чем спрятать ее в ящике для инструментов.
Магазинная техника: Схемы затяжки
Если деталь крепится более чем двумя застежками, важно чередовать затяжку между ними. Вот правильная процедура: закрутите все болты или гайки на несколько витков, а затем затяните их от руки. Часто в руководстве по ремонту указывается конкретная последовательность затяжки. Слегка затяните вручную, затем до момента затяжки 9.0003
1. Болты по кругу, как правило, зажимные гайки на колесах, следует затягивать не по кругу, а крест-накрест или по схеме «звезда».